Sabemos que aproximadamente dos tercios de los proyectos de construcción que se inician cada día en nuestro mundo generarán retrasos y sobrecostes a lo largo de la ejecución de su obra. Por desgracia el proyecto Ballerup (Dinamarca) formaba parte de este “selecto” grupo. La detección automatizada de desviaciones juega un papel clave en la inspección de obra para evitar estas situaciones.
El equipo arquitectónico del proyecto (Rubow Arkitekter) había planificado un nuevo complejo para su centro de salud mental de última generación que incluía cinco edificios con estructuras de acero. Ninguno de los edificios era igual, de hecho, el mayor parecido estribaba en la abrupta inclinación del revestimiento de madera que existía en el techo de cada estructura.
Cada cubierta tendría en su parte inferior múltiples placas trapezoidales prefabricadas en madera y, por otro lado, la parte superior se conformaría utilizando segmentos de metal corrugado atornillados a la parte superior de la estructura de vigas de acero.
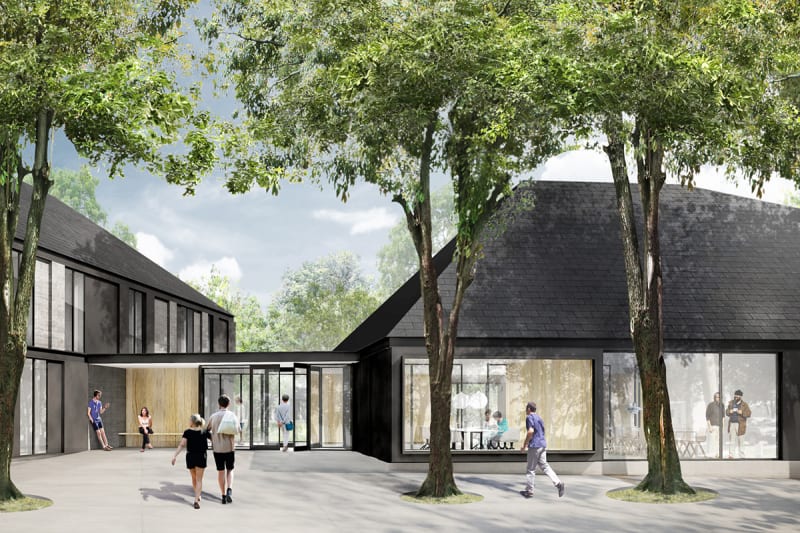
El problema: La instalación de cada sección de techo del primer edificio llevó horas en vez de minutos
Para resolver el problema derivado de la instalación de las vigas prefabricadas, el promotor contactó con una empresa de servicios de ingeniería y construcción especializada en escaneo 3D y modelado BIM.
Ambas partes debatieron y teorizaron sobre la dificultad encontrada a la hora instalar dichos segmentos. La teoría principal indicaba que las dificultades estaban relacionadas con una instalación imprecisa de las vigas de acero donde cada segmento de metal debía ser anclado. Dado que la estructura del primer edificio presentaba una desviación significativa respecto al modelo planificado, se sospechaba que los otros cuatro también estarían afectados de la misma manera, por tanto, por tanto, fue necesario detener la construcción mientras se estudiaban nuevas acciones.
La solución: Software para la detección automatizada de desviaciones e inspección de obra.
Esta empresa responsable de la nueva inspección de obra consideró necesaria la aplicación de un nuevo software de verificación de construcción automatizado, cómo hoy en día podemos hacer también con Checktobuild a través de su software para inspecciones plataforma C2B.
El software analizaba nubes de puntos tomadas con láser escáner del proyecto ejecutado y las comparaba con los modelos arquitectónicos planificados para determinar la precisión de los elementos construidos. La herramienta de análisis destacaba por identificar los elementos fuera de tolerancia, incluyendo detalles de medición específicos sobre errores en la ejecución y otros posibles errores como rotación, torsión y pandeo.
El flujo de trabajo: Escanea, verifica, repite.
Aunque se plantearon diversas opciones como escáner 3D y lidar, finalmente el equipo contratado usó un láser escáner para recopilar modelos 3D desde el interior, el exterior y desde la parte superior de cada estructura, repitiendo este trabajo en cada uno de los 4 edificios restantes, generando cuatro nubes de puntos individuales.
Obtuvieron un modelo CAD del diseño de la estructura de acero para comparar las nubes de puntos ejecutadas. Acordaron una tolerancia de 10 mm como desviación y posteriormente se analizó cada viga de forma individual para identificar si los elementos se encontraban en un umbral superior a dicha tolerancia respecto a su posición planificada a lo largo de los ejes x, y o z. El software verificó incluso zonas combadas de manera imprevista, torsiones o posible pandeo.
El uso de nubes de puntos tomadas por láser escáner y procesamiento con el software mostraron que el 70% de las vigas de acero se instalaron fuera de la tolerancia permitida.
El software generó un informe gracias a las inspecciones de obra, el cual mostraba un análisis de cada viga con detalles de sus mediciones y la desviación de cada uno de dichos elementos (fuera de tolerancia) con respecto a su ubicación planificada.
Posteriormente, esta información fue proporcionada al promotor para evaluar qué desviaciones eran aceptables y cuáles no. Encontraron zonas curvadas y secciones con torsión en aproximadamente ocho vigas de la armadura del techo. Esto provocó que los segmentos del techo del primer edificio no se pudieran instalar correctamente generando por tanto el importante retraso de todo el proyecto.
La conclusión: El software identificó las desviaciones que podrían corregirse antes de que los trabajadores de la cubierta regresaran y se enfrentarán a más retrasos y sobrecostes.
Se encontraron curvas y combaduras similares en un segundo edificio de los que estaban sin terminar, por lo que el promotor convocó una reunión con el instalador de las vigas para decidir la mejor manera de solucionar los problemas antes de retomar los trabajos de la cubierta.
Con todo ello, tanto el promotor como el equipo de inspecciones, verificaron que la contratación de la herramienta de detección automática de desviaciones desde el inicio del proyecto hubiese sido un factor diferencial para generar ahorro operacional. De este modo, también se han podido detectar los errores en elementos hormigonados. De hecho, si hubiesen detectado este problema antes hubiera sido mucho menos costoso retrasar la ejecución para evitar que se iniciara el costoso trabajo del equipo de cubiertas evitando por tanto importantes sobrecostes.
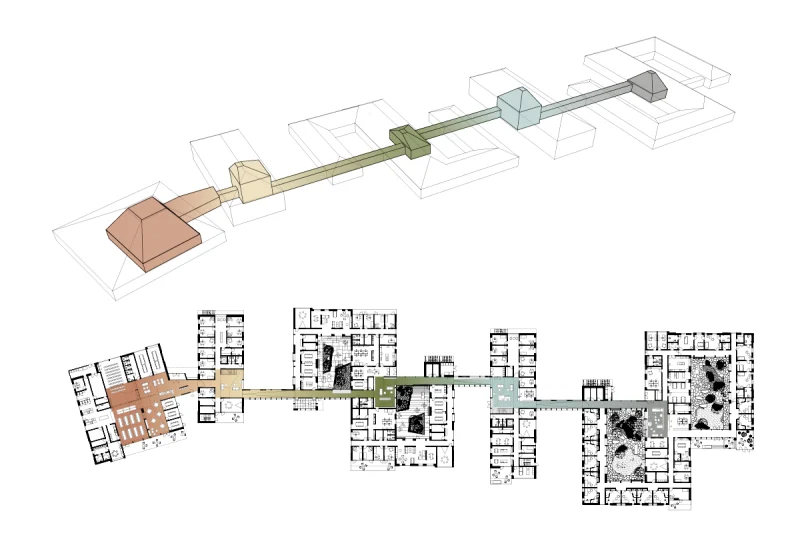